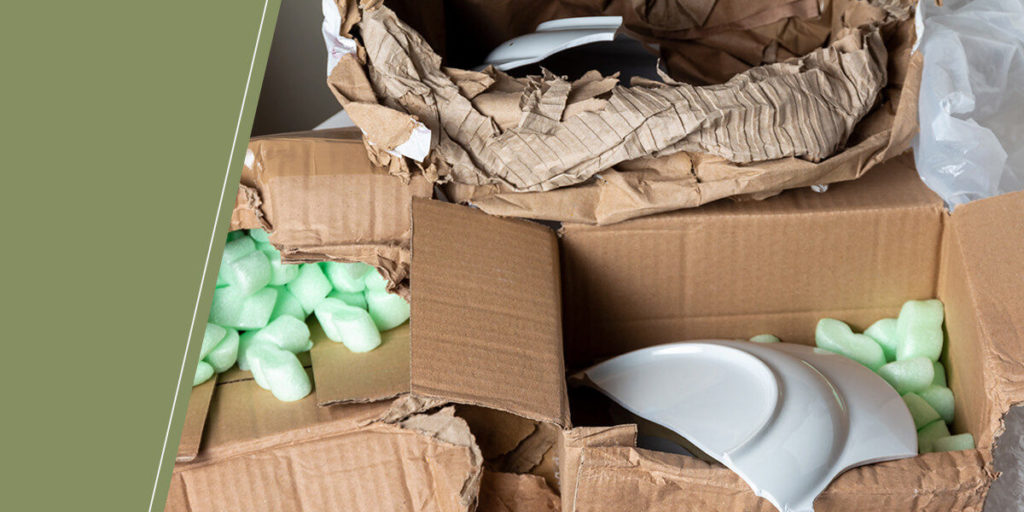
Certain products are more prone to damage during shipment than others. If you frequently ship fragile items, you may be looking for a packaging solution that can withstand the impacts, vibrations, compression and temperature changes of transit.
Use this guide to determine which items are most vulnerable during shipping and how to package them to reduce their chances of shipping damage.
Table of Contents
- What Items Break The Most During Shipping?
- Common Causes for Shipping Damage
- The Consequences of Shipping Damage
- How to Prevent Shipping Damage
What Items Break the Most During Shipping?
While any product shipped in the mail is susceptible to damage, those that are fragile or delicate are particularly at risk. The following items commonly break in transit.
Glass Items
Glass items are vulnerable to breakage during shipping, especially if their packaging is subpar. Standard boxes won’t always protect glass containers or objects from the bumps, drops and tosses they encounter while in transport. They can break, shatter or get scratched from repetitive movement.
If you use glass containers such as jars to ship your products, you’re likely familiar with transportation damage. However, you can take a few measures to protect glass during shipping and ensure your customers receive their products in good shape.
A smart place to start is by labeling the package. Brightly marked “Fragile” or “Do Not Drop” labels can alert handlers to treat your packages with care. Apply them to multiple sides of the box to ensure they don’t get missed.
You’ll also want to pack glass with enough buffering and cushioning material to stay secure through the rigors of transit. Glass containers that are wrapped tightly with sturdy layers of material can absorb impacts without breaking.
Learn More About Our Custom Packaging Solutions
Electronics
Electronics often get damaged or broken during delivery due to their awkward shapes and fragile construction. Rough handling, extreme temperatures and moisture all pose a threat to electronics during shipment.
Computers, televisions, smartphones, cameras and other devices contain intricate parts and components that aren’t designed to handle adverse conditions. For example, moisture inside the product can result in malfunctioning parts.
You can avoid these pitfalls by packing your electronics in water-resistant containers with plenty of padding and minimal extra space.
Furniture
In today’s flourishing online furniture market, everything from sectionals to antique cabinets makes its way through logistics. However, furniture isn’t immune to the sometimes rough conditions present during shipping. Often, packers don’t wrap furniture properly due to its size, leaving it vulnerable to scuffs and chips.
Just as with most other items, you should wrap furniture tightly with multiple layers of padding before being boxed up. If you must ship the product in various pieces, wrap each one separately. Packaging should be sturdy and only slightly larger than the products inside.
Alcohol Bottles
Alcohol bottles are often glass and prone to breakage if they get dropped or shift inside their boxes. Alcohol typically ships with multiple bottles in a package, and if there’s space between them, they can bump into each other and shatter.
The best way to pack alcohol bottles for safe shipping is to ensure there’s no extra space in the box for them to move around. Bottles should be separated with inserts and wrapped tightly with bubble wrap. It’s also a good idea to double-box alcohol bottles for an added layer of protection. Lastly, be sure to use sturdy, corrugated boxes that can support the weight of the bottles.
Musical Instruments
In addition to being fragile, musical instruments are often large and irregularly shaped, making it difficult to package them securely. String instruments like guitars are particularly at risk because they feature lightweight wood that can shrink or expand in extreme temperatures.
To minimize the risk of shipping damage, pack instruments in hard cases designed specifically for each instrument. Place the cases in sturdy exterior packaging, and be sure to label the packages accordingly as “Fragile.”
Common Causes for Shipping Damage
Aside from some objects being naturally susceptible to damage during shipping, other factors can increase the risk that your items will become damaged in transit:
- Items aren’t in proper packages: If products don’t have a sturdy container with adequate cushioning, they’re at risk of damage
- Empty space in the box: Items can bump against the sides of the package if there’s too much extra room
- Exterior packaging comes in contact with moisture or liquids: Moisture can damage the integrity of the packaging if it isn’t waterproof
- Couriers mishandle packages: You can combat this issue by labeling your containers with the appropriate labels to warn couriers that fragile objects are inside
The Consequences of Shipping Damage
Consumers expect their purchases to arrive in working order, and damaged deliveries create the hassle of returning the items and waiting for a replacement to arrive. Customers don’t like to be inconvenienced, especially when they’ve paid for something. If they receive damaged products from your business, they may look elsewhere for future purchases.
Of course, you must pay to replace every item that becomes damaged in transit, whether by sending a replacement or refunding the customer. If you don’t package objects properly, you’ll see replacement costs increase, which will harm your business in addition to the loss of customers and reputational damage you might experience.
How to Prevent Shipping Damage
Although some of the factors contributing to shipping damage are out of your control, using a customized packaging solution is the best way to ensure your products are as safe as possible.
Great Northern Fiber Interior Packaging uses 100% recyclable pulp to create custom interior molds that fit securely around your product. Our molds are a sustainable, cost-effective alternative to other packaging materials like foam or airbags. They’re also quick and easy to load, which may help you save money on time and labor.
Another way to prevent shipping damage is to have your packaging tested. Great Northern has a certified ISTA test lab that can determine if your packaging can withstand the rigors of shipment or if modifications are needed. We test your packaging by placing it in scenarios that simulate delivery conditions. If it doesn’t perform under these circumstances, Great Northern’s Fiber Interior Packaging can help.
Our interior packing solutions are suitable for any large, heavy or oddly shaped product. We mold packaging to fit your products, so you can expect optimal cushioning that keeps your items secure during delivery.
Great Northern Is Your Source for Custom Interior Packaging
Great Northern Fiber Interior Packaging offers packing solutions tailored to your unique products. With our innovative molds, your products can safely reach your customers in pristine condition. Contact Fiber Interior Packaging today to get started on a custom packaging solution that eliminates shipping damage.