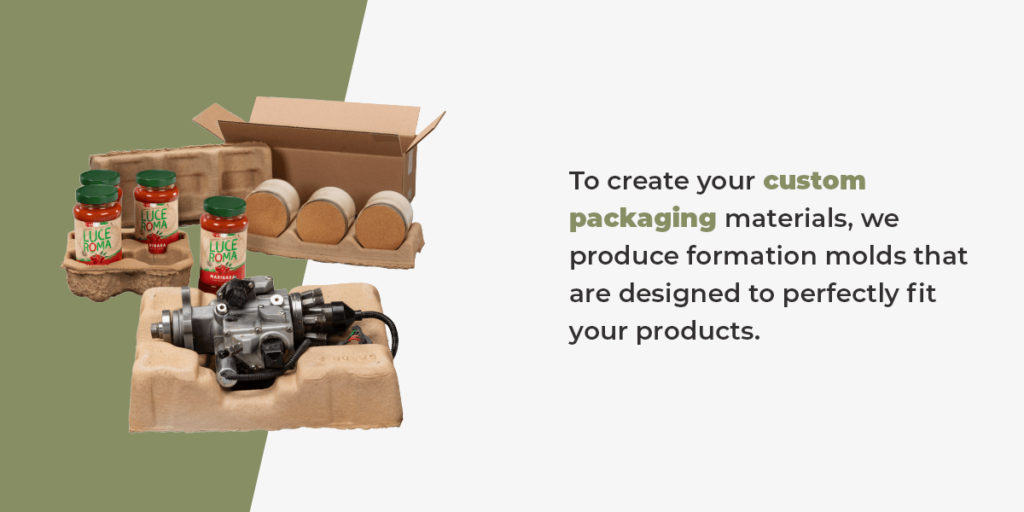
At Great Northern Fiber Interior Packaging, we create sustainable custom molded packaging solutions designed to protect your products during transit. These unique interior packaging materials are made from molded pulp, which is recyclable and 100% biodegradable.
Read on to learn more about how molded pulp is made.
Table of Contents
- What Materials Are Used?
- How We Transform Our Material into the Ultimate Packaging Solution
- Created Custom Molded Packaging with Fiber Interior Packaging
What Materials Are Used?
Our custom-molded pulp packaging begins with a variety of recycled, fibrous materials, including newsprint and used corrugate — recycled corrugated cardboard. These materials are combined with water to create a zero-waste slurry that comprises our molding material.
How We Transform These Materials
To create our pulp slurry, we soak the recycled materials in hot water to soften them up. Then, we put them into a machine that blends them together. The fibers of the materials swell up and break apart, allowing them to come together in a cohesive oatmeal-like consistency.
We run this slurry through a screen to filter out any plastics or other contaminants that may have gotten mixed in. The resulting pulp is what we use to create your custom interior packaging.
Creating Custom Molded Packaging
Unlike standard cardboard boxes that begin as flat sheets, our finished molded pulp packaging materials have round corners and complex three-dimensional shapes.
To create your custom packaging materials, we produce formation molds that are designed to perfectly fit your products. These molds can be any size or shape needed to protect your products properly. Fiber Interior Packaging uses a thick-wall molded pulp manufacturing process, which means we create our packaging using a one-part mold with mesh lining.
We place your custom-shaped molds in our pulp slurry, and a vacuum pulls the pulp through the mesh. This suction compresses the material and binds the fibers together. Once the pulp material is the desired shape, the mold is removed and the packaging material goes through an oven.
The oven dries out the packaging, evaporating the excess water and further bonding the fibers to create one solid piece of cardboard-like packaging material. Because of our thick-wall molding method, each finished packaging part features a thickness of 3/16 inch to 3/8 inch with one smooth side and one rough side.
Learn More About Our Custom Packaging Solutions
Choose Fiber Interior Packaging for Your Molded Pulp Packaging Needs
Protect your products and the environment with recycled molded pulp packaging from Fiber Interior Packaging. We work with you to create packaging tailored to fit and protect your products during transit, replacing less sustainable packaging materials. Contact our team today to start creating your custom molded packaging materials, or give us a call at 800.925.2626.