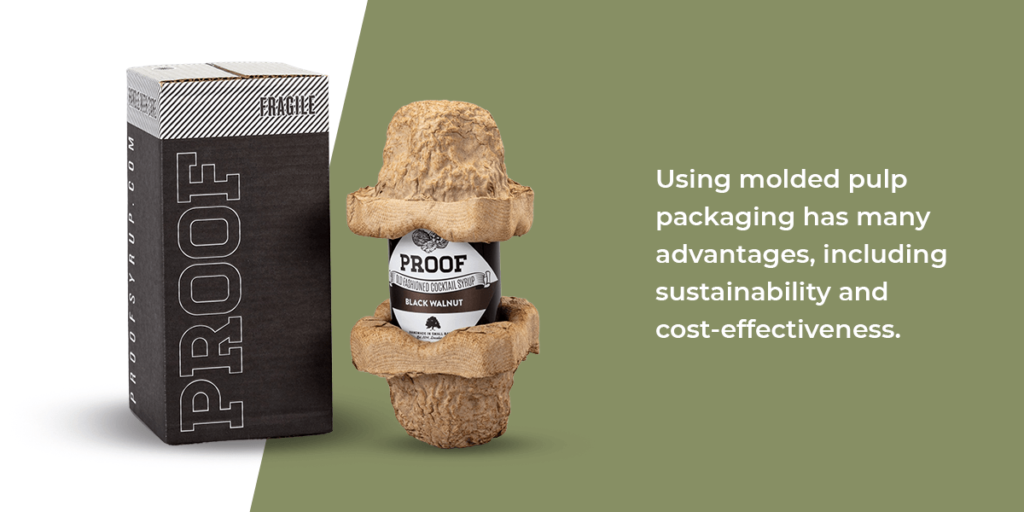
Fiber interior packaging, made from molded pulp, is a sustainable packaging solution. It can be customized to the shape of your product to provide optimal protection during transportation. Find out if molded fiber packaging is right for you.
Table of Contents
- What is Molded Fiber Interior Packaging Used For?
- What Is Molded Pulp?
- Types of Molded Fiber Packaging
- How Molded Fiber Packaging Is Made
- What Are the Benefits of Molded Pulp Packaging?
- Fiber Interior Packaging Tests Your Molded Fiber Packaging
What Is Molded Fiber Interior Packaging Used For?
Because molded fiber packaging can be formed to fit the shape of a particular product, many different industries use molded fiber packaging designs for shipping. In addition to shipping, molded pulp has many other uses. For example, the industrial sector uses it as packaging for consumer goods such as cell phones and vehicle parts, and the medical industry used molded fiber packaging for items such as single-use bedpans, urine bottles, and kidney dishes.
What Is Molded Pulp?
Molded pulp manufacturing combines fibrous material, including recycled paper, cardboard and other fibers. This mixture then gets molded into the desired shape through the manufacturing process. Molded fiber products created from waste paper or natural fibers allow them to be biodegradable and compostable.
Learn More About Our Custom Packaging Solutions
Types of Molded Fiber Packaging
There are several types of molded fiber packaging. Here are some of the most common:
- Thick-walled: This type of molded pulp packaging is oven-dried and has a wall thickness between 3/16 and 3/8 inches. Typically, one side is smooth, while the other side is rough. Thick-walled packaging gets used to transport heavier, non-fragile products, such as vehicle parts, furniture and flowerpots.
- Transfer molded: Transfer molded, another type of oven-dried molded fiber packaging, is manufactured using one forming mold and one transfer mold to produce packaging with walls between 1/8 and 3/16 inches. Both sides tend to be smooth. This type is most commonly used for egg cartons and trays but may also protect electronic product packaging, furniture, and glass jars during shipping.
- Thermoformed: Also called thin-walled, this type of packaging is manufactured using one forming mold and one transfer mold with product wall thickness between 3/32 to 5/32 inches. The smooth surfaces are detailed with minimal draft angles. These packaging pieces get dried in the mold with no oven curing.
- Processed: This refers to molded fiber packaging that needs a secondary treatment after getting molded and cured. This can include hot or after pressed, which adds print or color. The other secondary treatment may include special slurry formulations which add design features.
How Molded Fiber Packaging Is Made
Making molded fiber packaging takes several steps:
- Mixing: The raw materials are soaked in water and mixed until the pulp is the right consistency. During this process, all the excess water gets returned to the system.
- Forming: Custom-designed mesh tools form the packaging. These tools lower into the pulp mixture, and the water gets pulled through the mesh with a vacuum. The upper tools press the lower tools to shape the pieces. Suction from the vacuum binds the fibers.
- Drying: Most pieces get oven-dried on large open drying racks. Thermoformed molded fiber packaging dries with high temperatures and pressure in the mold.
- Pressing: When the pieces dry, the surfaces may become uneven. To remedy uneven sides, the sides get pressed onto solid metal tools. This improves the appearance and usability of the products.
- Trimming: The unneeded, excess parts of the packaging get trimmed and returned to the pulp mixture to get reused.
- Testing: The packaging undergoes quality testing to ensure it will protect the products it will package.
Benefits of Molded Pulp Packaging?
Using molded pulp packaging has many advantages, including sustainability and cost-effectiveness. Here are the top benefits of molded fiber packaging:
- Sustainable: As an eco-friendly solution, molded fiber is an excellent alternative to plastic packaging. Packaging constructed from recycled paper is 100% biodegradable, giving you peace of mind that your packaging is not going straight to a landfill, and is cutting down on disposal costs. Molded pulp packaging, when created from recycled materials, such as post-consumer cardboard boxes and newspaper, saves energy and raw materials.
- Customizable: You can customize molded fiber packaging into any shape you need. Create custom retail packaging that will fit your product perfectly and provide optimum protection for your product during shipping.
- Saves time and money: Using molded pulp for shipping saves time and money by reducing labor costs due to ease of use. Our custom-molded fiber packaging solutions are a “drop and go,” solution to help save packaging time. All you have to do is insert the bottom piece, place your products into the mold and insert the top piece. Other packaging options take more time and are more hassle. For example, with bubble wrap, you have to measure and cut the wrap, individually wrap each product and secure the products in the box. Corrugated inserts also take time to put together to package products properly.
Molded pulp packaging is sustainable and customizable. It can decrease labor and ultimately reduce your costs.
Fiber Interior Packaging Tests Your Molded Fiber Packaging
When you ship products, you want to have confidence that they will get to their destination undamaged. During shipping, your products will face less than optimal conditions. At Great Northern Fiber Interior Packaging™, we have the ability to test your packaging to ensure your products are protected. Ensuring your products make it to their destinations undamaged benefits your brand reputation and increases the likelihood of repeat customers.
The series of tests we run your packaging through helps us determine if your packaging is optimally designed or if we need to make modifications. We can test to ensure your product and packaging can withstand conditions such as vibration, incline, material handling, free-fall drops and compression.
Make the Switch to Molded Fiber Packaging
If you are looking for a sustainable, time and labor-saving packaging option that will reduce your carbon footprint, you’ve come to the right place. At Fiber Interior Packaging, we meet customer challenges with an undying spirit for doing what others can’t or won’t. It’s in our DNA. And it is what our customers have come to expect. Contact us to get started designing your new molded fiber packaging today, or give us a call at 800.925.2626.