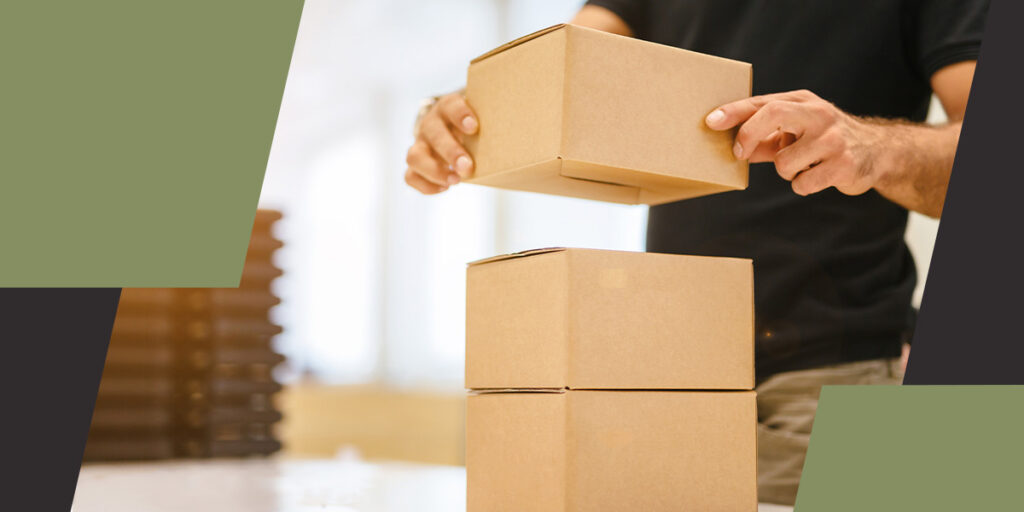
In the fast-paced business world, packaging plays a critical role. Aside from providing branding opportunities and ensuring products reach consumers free of damage, your packaging processes can actually speed up fulfillment.
Your packaging processes are a key factor in your supply chain efficiency. Optimized processes help ensure customers receive their orders quickly, which is essential for creating a good relationship with them.
Understanding the Role of Packaging in Fulfillment
There are several reasons to optimize your packaging processes:
- Avoid bottlenecks: Fulfillment efficiency begins in production — developing efficient packaging speeds up processes. Inefficiencies could result in bottlenecks. For example, if packaging is overly complex, it may take employees longer to assemble. When packaging isn’t the correct size, it could take up more space than necessary, creating crowded storage areas that are difficult to navigate.
- Reduce returns: Considering that total retail returns in the United States amounted to $743 billion in 2023, it makes sense to try and avoid as many of the reasons that lead to returns as possible. During the packaging process, you can reduce the chances of products getting damaged and having to process returns. Processing returns and sending replacements can cause delays.
- Prevent delays: Productivity issues, such as untrained workers and outdated equipment, affect delivery times. Better training programs and higher-quality equipment can speed up delivery.
- Meet customer expectations: Delays in assembling packaging could lead to delays in delivery and low customer satisfaction. By making packaging more efficient, you can improve your relationship with consumers.
- Gain a competitive advantage: Today, many businesses interact with consumers primarily online. When you do not have the opportunity to make that face-to-face connection, your fulfillment efficiency can help you establish trust. Reliable containers and speedy delivery times can give you a competitive advantage over other businesses offering similar products and services.
Assessing Your Current Packaging Process
The first step to packaging optimization involves assessing your current process to understand where you can improve. Here are three things to keep in mind:
- Analyze your current workflow: How is your current workflow, from order receipt to dispatch? Map the product journey from when it’s ordered to when it’s shipped.
- Identify bottlenecks: Multiple factors, such as complicated packaging and regulatory compliance challenges, can slow down packaging processes. Identifying these inefficiencies will help you streamline your packaging process.
- Measure your current performance: Tracking key metrics is the most effective way to identify and resolve inefficiencies. Data speaks volumes, so when you notice your packaging time per order or error rates are higher than you’d like, you can create a strategy for speeding things up.
Strategies to Optimize Packaging for Faster Fulfillment
Well-functioning packaging processes speed up fulfillment, which translates to greater customer satisfaction and better overall efficiency. Here are strategies to optimize packaging for faster fulfillment.
1. Study Your Product and Use the Right Materials
Optimizing your packaging process begins with examining the product itself. What are its needs and vulnerabilities? Is it fragile, high-end or does it need to remain fresh? Studying the product allows the design team to create packaging that protects the product without affecting your team’s efficiency. Ideally, you want to use materials that are easy for your employees to pack, sort and store to reduce bottlenecks and delays.
2. Test Your Packaging to Prevent Damage and Returns
Processing a high volume of returns and sending replacements can impact fulfillment speed. To reduce returns resulting from product damage, you need to know that your packaging can handle the conditions of the supply chain. The best way to do so is to get it tested.
Advanced tests replicate the shipping environment and challenge your container’s capabilities. A certified International Safe Transit Association (ISTA®) test lab can help determine whether your packaging can withstand difficult conditions by exposing it to vibrations, inclines, free-fall drops and other challenges.
3. Simplify Your Packaging
With your inventory growing, you may find that you’re dealing with a large number of packaging products and materials. As a result, your packaging processes might get slower. You can get things back to normal by simplifying your packaging. For example, you can prioritize using fewer materials, lighter materials or simpler packaging designs.
4. Implement Standard Operating Procedures (SOPs)
Standard operating procedures (SOPs) are a set of written instructions that ensure consistency. To reduce packing times and enjoy the associated benefits, your packaging process SOPs should include:
- Materials and equipment needed.
- Detailed steps for packaging products.
- Storage and handling guidelines.
- Safety considerations.
- Training requirements for employees.
- Documentation guidelines.
With SOPs in place, you’ll notice increased output and faster operations, which are crucial in shipping and packaging optimization. You can review your plan regularly to make updates as needed.
5. Optimize Your Workspace Layout
Small changes to your operations, like adjusting the packaging station, can have a significant impact on workflow. Optimize your workspace by designing an ergonomic packaging station that minimizes movement and improves access to the most utilized supplies. You also want to declutter and encourage better organization to make the space easy and comfortable to work in.
6. Invest in Automation
Automation has transformed how many businesses operate, providing a unique way to meet customer demands. With automation, companies can complete labor-intensive processes and tasks quickly. Automated systems, such as labeling machines and conveyor belts, can significantly boost packaging efficiency.
Factors that slow down the packaging process may no longer present an issue once you introduce automation. Investing in the latest technologies can help speed up time-consuming tasks and achieve packaging efficiency.
7. Provide Training and Skill Development
Training is more crucial than ever, as some worker skills may become outdated due to emerging technologies like artificial intelligence. Regular training improves current skills and keeps your workforce up to date with new trends, technologies and best practices, ensuring speed and accuracy.
Best Practices for Continual Improvement
Continuous improvement allows businesses to refine their processes, keep up with industry trends and process orders fast for quick fulfillment. Here are some of the best practices to foster improvement in packaging processes:
- Conducting process audits: Certain processes and tools become outdated as new methods emerge. Inefficiencies may also creep in due to productivity issues. Conducting periodic reviews of packaging processes helps identify areas for improvement.
- Adopting a lean approach: Lean principles aim to eliminate wastage in company operations and enhance efficiency. Use the principle to analyze and remove unnecessary tasks in packaging operations.
- Promoting team feedback: Feedback is a vital aspect of growth. The people on the ground understand a company’s day-to-day challenges and can offer valuable insight. By involving employees in the optimization process, you can foster a culture of continuous improvement.
- Keeping up with industry trends: Technology is at the forefront of modern business operations, streamlining workflows and enabling businesses to speed up their processes. Leveraging the latest packaging technologies and trends will help improve process efficiency and keep your business competitive.
Improve Your Packaging Process With Great Northern
Fine-tuning your packaging process leads to overall fulfillment optimization, which makes paying attention to your packaging decisions essential. Every choice you make impacts your efficiency and, most importantly, customer satisfaction. Refining your strategies and tapping into innovative solutions like custom-molded fiber protective packaging can be the key to optimizing your packaging process.
Great Northern Fiber Interior Packaging specializes in innovative custom packaging solutions. We understand the need for effective packaging that matches your product needs, and our certified ISTA® 6 Test Lab can ensure your packaging is designed optimally. Our packaging solutions are also quick and easy to load into shipping boxes, making them an excellent choice to speed up your packaging process and get your products into the hands of customers faster.
Get in touch today to learn more about our process and discover how molded fiber packaging can streamline your supply chain.