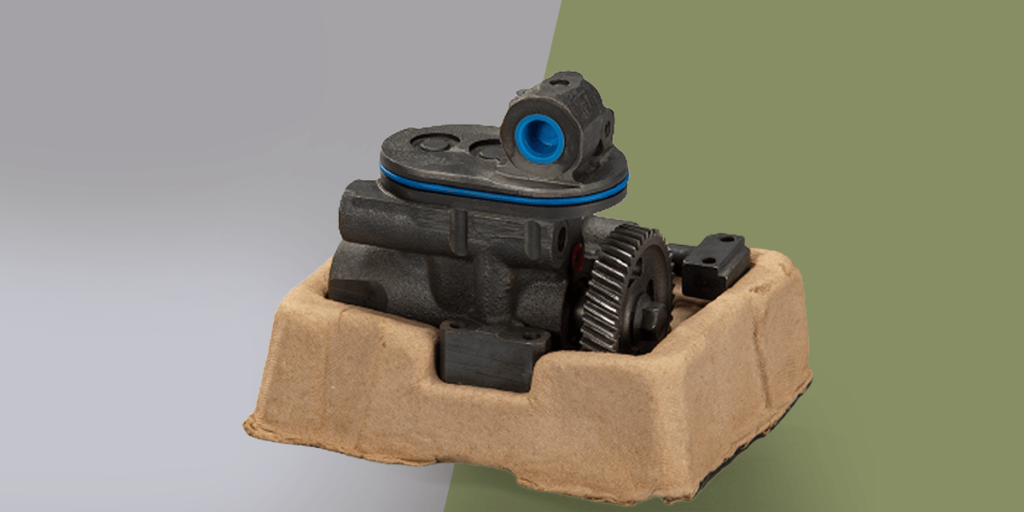
There’s a packaging solution revolutionizing the shipping industry! Molded fiber packaging is a leading, innovative material that diversifies what’s possible when shipping products. This material has an edge over other solutions like foam because it can match individual product shapes. Molded fiber is common with lightweight objects, but how well does it perform with heavy items like automotive parts?
To ensure performance, heavier goods like automotive components must reach their destination intact. This guide evaluates the compression strength of molded fiber packaging to determine how well it handles weightier items without falling apart.
What Is Compression Strength?
Compression strength refers to a material’s ability to withstand forces that try to reduce its size. It contrasts with tensile strength, which measures a material’s ability to resist forces that attempt to stretch it. In simple terms, compression strength deals with forces that compress or squash a material, while tensile strength deals with forces that pull or stretch it.
How Compressive Strength Affects Packaging Materials
The compressive strength of packaging materials varies depending on factors such as:
- Material type: Different packaging materials respond to compression differently depending on their inherent characteristics. Some materials have higher compression strength than others, but they may lack qualities that make them ideal for packaging, such as cost-effectiveness and sustainability.
- Quality: The quality of a specific material can impact its ability to resist compression. With fiber packaging, the combination of high-quality materials provides reinforcement, enhancing compressive strength.
- Production process: Different production processes and environments can impact a packaging material’s compressive strength, which is why testing is important to ascertain reliability.
What Is Molded Fiber Packaging?
Molded fiber interior packaging is a specialized material made from corrugated, newsprint and other fibrous materials and used as a custom-fit protective insert. It’s an innovative solution offering a reliable alternative to traditional packaging insert materials such as molded foam, corrugated and bubble wraps, which have unique disadvantages that may impair your process and bottom line.
For example, while molded foam can be custom-fit like molded fiber and remains consistent, it’s bulkier and has a negative impact on the environment. Also, unlike molded fiber, options like honeycomb and bubble wrap are labor-intensive, bulky and not practical for customization.
Benefits of Molded Fiber Packaging in Shipping
Molded fiber packaging has several advantages that make it an ideal material for shipping. Here are some of the key benefits:
- Reliable: Damaged or defective product was the biggest reason for e-commerce returns in the U.S. in 2022. This data emphasizes the importance of packaging because the shipping process exposes products to conditions that can cause damage or impair product quality. Fiber inserts provide cushioning and a perfect fit, creating a stable and reliable environment that minimizes the risk of damage while in transit.
- Customizable: Molded pulp technology used in manufacturing fiber interior packaging offers 100% customization. That means the inserts are tailored to meet the specific needs of your product, accommodating the shape you need for maximum protection during shipping. Remember, the flexibility with diverse shapes doesn’t impair quality. Fiber packaging maintains sturdiness while also providing a perfect fit.
- Versatile: Fiber packaging is suitable for a broad range of products across multiple industries. These include small containers, power tools, automotive parts and accessories, exercise equipment and more.
- Sustainable: With many consumers turning to environment-friendly solutions, sustainability is becoming critical in all aspects of production. Molded fiber has a fully sustainable life cycle and offers an excellent alternative to foam and plastic, which are not biodegradable and can be hard to recycle. Since the raw material for molded fiber is recycled paper and cardboard, it’s 100% recyclable and naturally breaks down in the environment.
- Cost-effective: The use of molded pulp in packaging creates opportunities for cost-cutting. Due to its “drop and go” simplicity, it can save packing time and minimize labor costs. Since the inserts are already designed to accommodate products, there is no need for assembly or additional packing skills like measuring and cutting. All you have to do is drop your product inside the mold for secure packaging.
Why Compressive Strength Matters in Fiber Packaging
Compressive strength is critical in molded fiber packaging as it determines how the material behaves under diverse conditions that simulate real-life scenarios. For composite materials like molded fiber, compression strength is an ideal parameter that influences performance and durability.
With fiber packaging gaining popularity for heavier objects like electronics and automotive components, reliable providers are investing in ways to improve molded fiber compression strength, ensuring that packaging can withstand forces present in the supply chain.
Testing Compressive Strength in Fiber Packaging
Manufacturers employ different testing methods to determine molded fiber compression strength. In the U.S., standardized methods for testing compressive strength are established by agencies like the International Safe Transit Association (ISTA) and ASTM International. These tests follow clear procedures for stress application to ensure the material can withstand real-life environments such as compression, handling, vibration, incline and free-fall drops.
Why You Need High-Strength Fiber Packaging
Custom molded fiber packaging is a unique material with compelling benefits, making it an attractive alternative to common solutions like foam and bubble wrap. Besides its cost-effectiveness, it appeals to modern consumer demands for sustainability without compromising quality and effective product protection.
Molded fiber offers a practical approach to product protection as you can customize it into diverse shapes to cradle your product for secure shipping. The strong and custom-fit construction allows the material to absorb shocks and vibrations while minimizing movements, which reduces the risk of damage. These qualities can help lower costs, reduce product returns and promote your brand.
Explore Molded Fiber Packaging at Great Northern
The emphasis on high-quality packaging is growing, especially in the automotive industry, where slight defects in parts could render them ineffective. Molded fiber is a reliable protective packaging solution with various qualities, such as strength, versatility and sustainability.
If your current protective packaging doesn’t adequately protect your products, consider superior-quality molded fiber from Great Northern Fiber Interior Packaging. We offer innovative and frustration-free packaging that takes the stress out of packing, minimizes the risk of damage and streamlines your shipping.
If you’ve been searching for a secure way to pack your items, work with us to develop a custom packaging solution you can count on. Contact us today to discuss your product and find a long-lasting solution!